Problemas no sistema de ar comprimido: uma grande oportunidade de redução de consumo de energia e economia
JS
Como calcular os custos do ar comprimido?
Fórmula básica para o cálculo:
Custo anual = potência do compressor em kWh x 8760 horas trabalhadas x Custo do kWh R$ 0,35 dividido pela Eficiência do motor de 0,90 Por exemplo: 01 HP de um compressor em trabalho contínuo custa aproximadamente R$ 2.540,00/ano em energia elétrica.
Para descobrir o custo em sua indústria, multiplique a potência instalada em uso pelos seus compressores por esse valor e você terá o gasto anual de seus compressores.
Por exemplo: A soma das potências dos compressores que resultem 300 HP custará aproximadamente R$760.000,00/ano em energia elétrica. Se o valor de kWh e as horas trabalhadas forem diferentes, basta alterar na fórmula para se calcular o custo por HP.
Além dos custos de energia elétrica, há outros custos envolvidos:
- Equipamentos e acessórios (amortização)
- Instalações (amortização)
- Manutenções (partes e peças)
- Mão de obra envolvida (direta e indireta)
- Tratamento do ar comprimido (filtragem + secagem + drenagem + descarte)
Distribuição de custos de um compressor
Levantamentos realizados pelo C.A.G.I – Compressed air Gas Institute indicam que após cinco anos de trabalho os custos de um compressor são distribuídos da seguinte forma: 76% em energia elétrica e 24% em outros custos.
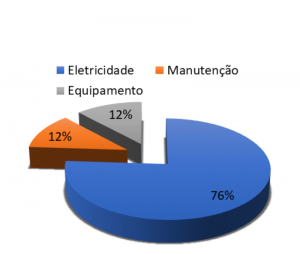
Partindo desse levantamento de distribuição de custos, podemos estimar que cada HP irá custar R$ 3.400,00/ano. Assim, o custo por m³ de ar comprimido é de aproximadamente R$ 0,055.
Podemos considerar, para efeito, de estimativas que cada compressor de 100 HP (75 kW) de potência, custa para gerar ar comprimido R$ 340.000,00/ano em energia elétrica, amortização de instalações e equipamento e sua manutenção para operação em bom estado.
Os custos envolvidos nas operações com o ar comprimido são costumeiramente negligenciados na gestão da indústria, o que resulta, inevitavelmente, num foco de desperdício na produção. Revelar e enfatizar esses custos é uma forma de conscientizar os envolvidos para o fato de que, embora numa olhada descuidada o ar comprimido pareça um recurso gratuito e infinito, na prática trata-se de um recurso que consome altas quantidades de energia elétrica e investimentos e gastos com manutenção e mão de obra. Isso tudo considerando que os compressores funcionem normalmente, o que então dizer dos custos quando há vazamentos, problemas técnicos ou desperdício na operação?
Estabelecendo a redução do consumo de energia
A economia tem início com uma avaliação diagnóstica minuciosa do sistema, onde serão identificadas cada oportunidade de redução e eficiência. Neste processo, leva-se em conta o panorama atual do sistema de ar comprimido em funcionamento, apontando somente soluções economicamente viáveis e de implementação imediata, que possam ser realizadas sem a necessidade de grandes modificações em equipamentos. Como o foco é redução, a estratégia aqui é otimizar o sistema existente.
Várias organizações, entre elas a ELETROBRAS/PROCEL, o CAGI – Instituto do Ar Comprimido e Gás dos Estados Unidos, Companhias de Distribuição de Energia Elétrica em todos os continentes e os fabricantes de compressores confirmam a estatística de que 43% do ar comprimido gerado é desperdiçado em demanda artificial. A experiência prática demonstra que às vezes esse porcentual é maior.
Para um compressor de 100 HP, o desperdício chega a R$ 90.000,00/ano ou aproximadamente 30 kWh de energia elétrica no sistema. Num cenário econômico altamente competitivo em que a eficiência é fator essencial para a sobrevivência da indústria, permitir um desperdício dessa natureza seria uma conduta irresponsável.
Corrigir essa demanda artificial significa que os prejuízos gerados por essa situação serão eliminados e que a economia resultante se tornará lucro, o que se torna possível com relativa facilidade e baixo investimento. E você saberá exatamente como.
O uso do tripé da reversão de desperdício de energia e dinheiro está baseado em:
- Treinamento
- Tecnologia
- Metodologia
1 – Treinamento
- Formar especialista em gestão de sistemas de ar comprimido.
- Conscientizar os usuários sobre os usos e custos do ar comprimido.
- Criar uma Comissão Interna de Controle de Energia (baseada na Norma ISO 50.001).
2 – Tecnologia (uso de equipamentos de precisão com registro de dados)
- Medir a geração e demanda de ar comprimido com equipamentos precisos.
- Consolidar dados sobre o sistema atual e estabelecer metas de redução considerando a otimização dos equipamentos em operação.
- Utilizar equipamentos de detecção ultrassônica para identificar, localizar e medir a intensidade e quantidade dos vazamentos.
3 – Metodologia
- Estabelecer critérios e objetivos claros para a aplicação do plano de melhorias, considerando a continuidade da produção concomitante às correções necessárias.
- Gerar relatórios detalhados sobre as soluções almejadas e estratégias de execução.
Localizando oportunidades de redução de consumo de energia
É comum que a equipe que atua nas áreas de utilidades e manutenção esteja ciente da existência dos problemas enumerados a seguir, mas sem treinamento, conhecimento e equipamentos adequados não são capazes de identificar e mensurar a economia que cada um deles pode representar:
- Vazamentos
- Excesso de pressão
- Usos inadequados/impróprios
- Excesso de temperatura na admissão do ar pelo compressor
- Drenagem de água inadequada/ineficiente
- Perda de carga em elementos filtrantes saturados
- Dimensionamento de redes e tubulações
Com treinamento, metodologia e tecnologia é comprovadamente possível reduzir o nível de demanda artificial e obter uma redução substancial no consumo de energia elétrica no curto prazo.
Veja o exemplo a seguir do que pode ser obtido para um compressor de 100 HP.
Objetivo planejado para redução de custos no sistema de ar comprimido: 15%
Cada oportunidade possui um potencial de contribuição para:
- Redução do consumo energético
- Capacidade de aplicação
- Viabilidade econômica
Já mencionamos o potencial de redução de consumo de energia fixado em 43%. Nossa experiência na implementação de inúmeros projetos confirma que este objetivo é perfeitamente possível, mas está distante da realidade imediata da maior parte das indústrias, uma vez que demanda soluções complexas e investimentos elevados. Considerando os desafios da indústria atualmente, definimos inicialmente uma meta de redução 15%, valor que é seguramente obtido com a aplicação do Tripé da Reversão (Treinamento – Tecnologia – Metodologia).
Após as medições e avaliações iniciais é feito um diagnóstico validando o objetivo de redução e economia de energia elétrica, imediatamente são definidos os objetivos individuais e ações correspondentes, como demonstra tabela abaixo.
Metas:
- Redução de 15% na geração de ar comprimido.
- Valor a ser economizado: R$ 35.000,00
Ação | % Redução | Economia (R$) |
---|---|---|
Eliminação de vazamentos com metodologia 20/80* | 10% | 23.000,00 |
Redução de excesso de pressão | 1,8% | 5.000,00 |
Eliminação de usos Impróprios/Inadequados | 0,5% | 1.000,00 |
Redução de perdas de carga | 0,5% | 1.000,00 |
Redução de temperatura na sala dos compressores | 1,2% | 3.000,00 |
Eliminação de perdas em drenagem de condensados | 1% | 2.000,00 |
Objetivo de economia a ser atingido | 15% | 35.000,00 |
*20% dos vazamentos representam 80% das perdas. |
Uma questão de prioridade
A respeito dos vazamentos é possível afirmar que a equipe de manutenção não apenas tem consciência da existência de sua existência e da necessidade de realização de reparos, como eventualmente tenta atuar para reduzir o desperdício.
A barreira para a ausência de solução efetiva é a necessidade da continuidade da produção. Já que redução de vazamentos não é uma diretriz estabelecida pela diretoria ou gerentes de áreas, a equipe de manutenção não tem autonomia para interferir no ritmo da produção. Não sendo uma prioridade, por sua vez, a equipe não tem muito interesse de mensurar e informar à diretoria o custo efetivo dos vazamentos e urgência do reparo. Dessa forma os vazamentos ficam de forma contínua gerando um prejuízo através de desperdício de energia elétrica indefinidamente.
Não basta saber o que fazer, é preciso saber como fazer
Nossa metodologia 20/80 de relatar os vazamentos é feita de maneira que a localização, identificação e intensidade represente uma parcela significativa dos vazamentos, com o maior valor das perdas existentes, facilitando a programação dos reparos.
A obtenção desse relatório só é possível com o suporte de equipamentos de alta tecnologia e um método de análise que reduza o número de ações de correção, mas que representem um valor significativo de economia e que possam ser executados dentro de uma programação rotineira, sem prejuízos à produção.
As correções de vazamentos representam baixíssimos investimentos e propiciam retorno imediato, mesmo quando incluída a mão de obra para a realização dos reparos em comparação com os prejuízos que causam. O retorno sobre o investimento é grande e ocorre em curto espaço de tempo.
Gestores especializados em sistemas de ar comprimido irão identificar as oportunidades e estabelecer o Plano de Melhorias para Alta Eficiência Energética do Sistema, que servirá de roteiro para que os objetivos estabelecidos sejam alcançados.
As demais soluções são diagnosticadas e relatadas através de uma análise pormenorizada do sistema por meio da qual são estabelecidas as prioridades na execução do plano de melhorias.
Em síntese, um plano de treinamento de baixo custo, equipamentos adequados para diagnósticos e uma metodologia que facilite a implantação dos planos de melhorias são a garantia de sucesso. Uma economia anual de R$ 30.000,00 para cada compressor com a potência de 100 HP está ao seu alcance, faça acontecer.
Monte uma equipe qualificada para as melhores práticas em ar comprimido, essa decisão impede a reincidência de desperdício de energia elétrica e consequente prejuízo. Com treinamento e qualificação sua equipe se manterá alinhada e funcionará como uma célula de redução de custos.
Treinamento assegura desenvolvimento e é fonte de qualidade em tudo que se produz.
Pay Back
O retorno do investimento de uma auditoria e consultoria para o sistema de ar comprimido, após a implantação de medidas básicas de correção, que podem ser efetuadas pela CBA também, é obtido em até 6 meses de economia de energia elétrica, tomando como base uma potência instalada de 200 HP produzindo ar comprimido.